Engine Builder and Engine Pro present Shop Solutions in each issue of Engine Builder Magazine and at enginebuildermag.com to provide machine shop owners and engine technicians the opportunity to share their knowledge to benefit the entire industry and their own shops. Those who submit Shop Solutions that are published are awarded a prepaid $100 Visa gift card. Submit your Shop Solution at [email protected] . You must include your name, shop name, shop address and shop telephone number. Submitted Shop Solutions not published will be kept on file and reevaluated for each month’s new entries. Related Articles - Shop Solutions December 2023 - Shop Solutions November 2023 - Shop Solutions – October 2023
Before installing cam bearings, make sure to chamfer any oil holes and clean up back grooves of any sharp edges. This is especially critical with aluminum blocks. I like to give these areas a little buff on the mounted wheel to finish. This will prevent pulling or peeling that could contaminate an oil galley. Rectangular Steel Tubing Sizes
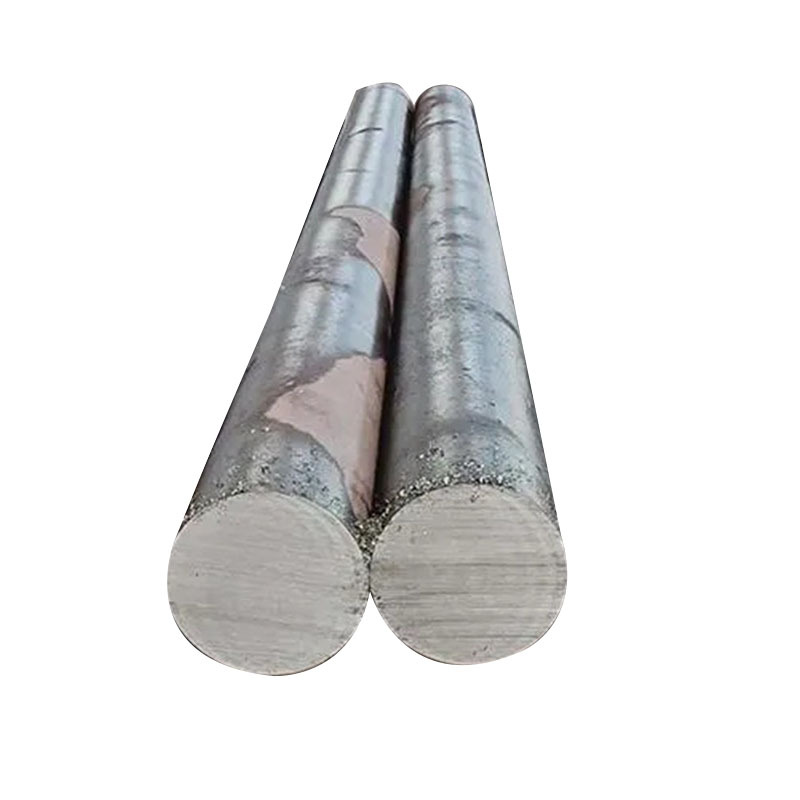
Ron Flood Cedar Machine North Branch, MN
When I need to mill something that’s hard to set-up and hold, I use this 19″ 3″x4″ 3/8″ thick angle iron. I just bolt on the head, ex manifold or whatever won’t work out on the machine’s mounting plate. I’ll mill slots for even more universal mounting if I make another one. Mine has many holes, slotted holes and whatever it takes to get the job done. I’ve even milled piston domes by setting them on a ring and a round bar thru the pin bore with a redi-rod threaded into that.
Randy Torvinen Torvinen's Machine Menahga, MN
I made this drill guide to quickly center existing lug stud holes when upgrading to larger lug studs in axles. To begin, the round bar needs to be approximately 2″ long, and approximately 1/4″ larger in diameter than the drill bit’s size. Drill 1″deep into the short length of steel round bar. Taper the other end ~10 degrees. To use, slide the tool over the drill bit, then insert the tapered end into the existing hole to accurately center the drill bit.
Tom Nichols Automotive Machine & Supply, Inc. Joshua, TX
We made our own reluctor wheel installation tool for LS engines, and it works like a charm. We used junk materials from around the shop, including an old valve stem, and have about 2 hours of labor into making it. A chunk of 1/2″ plate steel drilled to fit the flexplate/flywheel register on the crank, a valve stem that fits the locating hole on the reluctor wheel, and a pin that fits the blank hole on the flexplate/flywheel flange. It would be just as easy to make the same for other engines such as the Mopar Gen III Hemi.
Rich Jones Redline Automotive, Inc. Davie, FL
IT’S BETTER TO SUCK AT YOUR JOB
Sometimes, it is better to suck at your job instead of using an air blow gun to remove debris or chips away from your work piece. Using a vacuum will keep your work area cleaner along with reducing air borne irritants and possible eye damage. I rigged up this foot switch operated vacuum to save time and my back. I have placed a vacuum by every “dirty” machine, which encourages cleanliness without the hassle of moving one around the shop.
Josh Mitchell Mitchell Machine Works & Custom Neligh, NE
My head porter and I developed this tool to keep all valve job bowl cuts identical. Very simple to make and quickly scribes exactly where to make cuts. Scribe is made from a carbide point from pocket metal scribe. It is epoxied into a drilled hole in the adjusting screw. An assortment of cut valve stems allow the tool to be used in a variety of different guides.
Eric Gartner Performance Off Road Shadyside, OH
Engine and machine shop tips and tricks.
Regardless of the material, in time, humidity takes its toll. As such, many welding rods end up being trashed. Especially susceptible are aluminum, magnesium and chromoly. I keep my rods in hermetically sealed homemade tubes of plastic plumbing pieces to keep humidity out.
Engine and machine shop tips and tricks.
If I’m not using torque plates, I tape up both sides and trim out the bores. I use painter’s tape, which comes off easily and doesn’t leave any glue residue. I get much less oil in the spray washer this way.
Check out February’s shop tips and tricks.
Next time you have set of large journal small block Chevy connecting rods to resize, consider honing the big ends of them for a +.002” outside diameter bearing that the LS engines with fracture cap rods use.
Everyone misses occasionally, and this helps avoid dents and damage.
November tricks and tips for the shop!
When machining on the CNC mill, it’s necessary to blow the flood coolant and chips off the parts for inspection. I tried a tool holder mounted fan, but it wouldn’t get all the chips and coolant out of the deeper areas.
September tricks and tips for the shop!
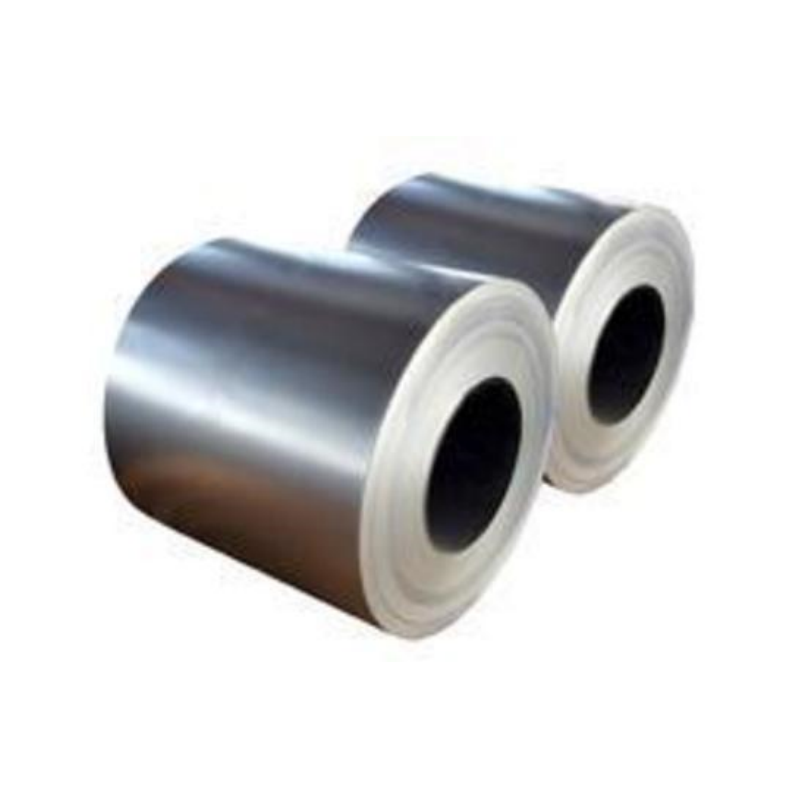
Roof Stainless Steel Content for engine professionals and enthusiasts